1
2
3
4
5
6
7
8
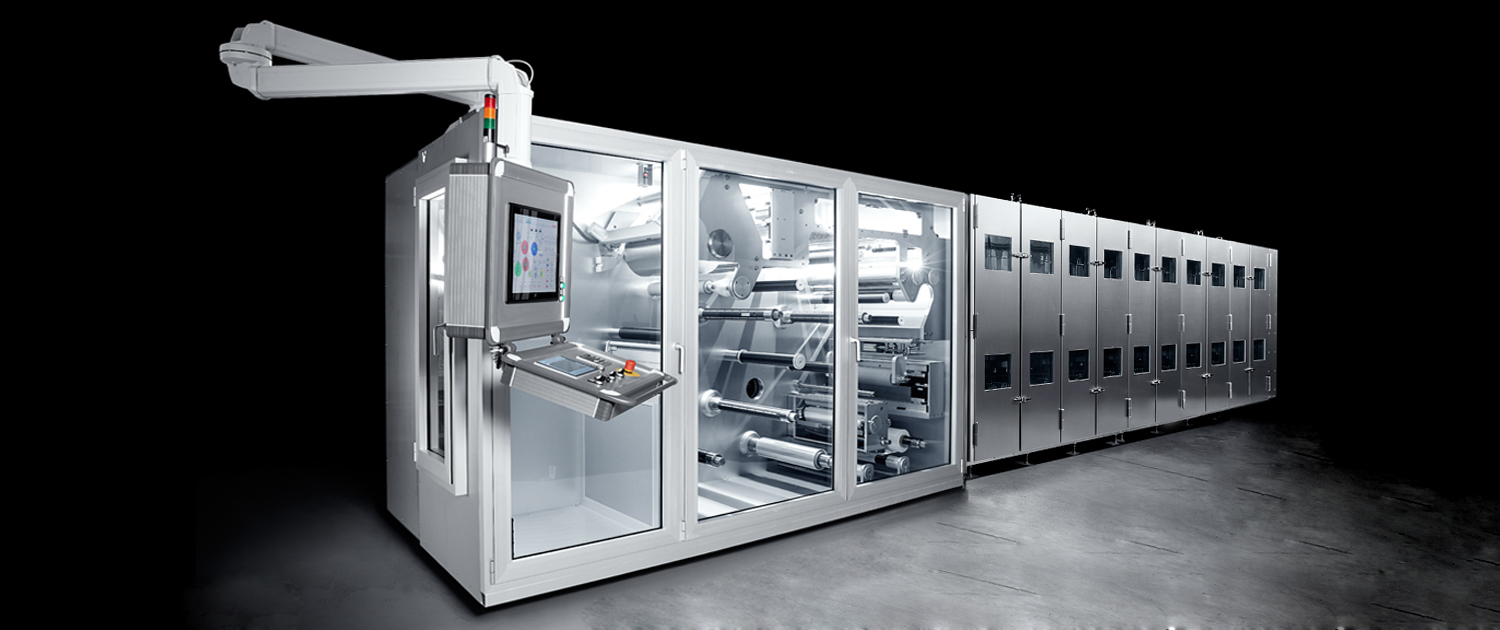
1
Our production machines run fully automated and only controlled by the touch screen HMI. Due to the swing comfort panel you can operate it from any point of the machine.
2
Our production machines are offered in 4 current foil widths: 460mm, 480mm, 540mm and 1200mm.
The foil width is choosen to match the subsequent converting process.
3
Our ultra-precise coating system will guarantee that you always have the precise dosis of your active pharmaceutical ingredient in your product and that you will always meet U.S. FDA standards. Especially when it comes to high potent drugs.
4
Our inline dry thickness measurement system carries out the quality inspection and testing while you can focus on producing your medicaments.
5
Our dryer is designed in a modular way. You can freely choose between: 2 drying zones, 4 drying zones, 6 drying zones, 8 drying zones, 10 drying zones and 12 drying zones.
The drying zones determine the production outputs and at the same it adapts to your space in the production area. Due to very good insulation of the dryer, you face lower energy costs than comparable dryers. Since the dryer is designed in a u – turn manner, operating costs will be minimized.
6
The cutting table is an additional tool and guarantees a precise positioning and connection of two foil endings.
7
Optional unwinder for membrane controls dosage release.
8
Oil coating station for the manufacturing of matrix patches. Membrane controls dasage release.
Commercial production coating machine PA 1200mm
The leading model
Application
The PA 1200 coating machine is designed for a large volume production of transdermal therapeutic delivery system lamination (skin patches) and edible films/ oral dissolvable film (mouth drug strips) bulk without any following modification. You can set the machines parameters and control the whole coating process with the touchable and flexible display. The coating system, which takes a leading role in the market in light of its high exactness, is suited to coating widths between 30 – 1180mm.
High capability
Nothing better than the leading machine in terms of efficiency. Its excellent output is 2,7 times that of PA 460/ 480 and 2,3 times that of PA 540 at the same dryer length. Clearly, with the modular system concept, you can also lengthen the dryer to increase your production volumes. The output of a machine with a dryer length of 22m is increased by 7 times compared to it adopted the 4,7 m dryer. In other words, you can find the products that are suitable for your production from two scales.
Self-regulating
The commercial manufacture machine is high efficient and intelligent alike. In view of that, all of our commercial production equipment can be controlled by one person with free hanging 19” comfortable touch panel mounted on a cantilever beam. The programmable logic controller (PLC) inside the electrical cabinets and the touch panel are for machine recipe/ control, visualization and so on, as well as internet/ intranet connection for remote control-and inspection.
Turnkey solution
We provide professional, knowledgeable choices for the individually designed machine. Other than that, we make the entire process from initial idea to enter service. Just go for the accessories to make full use of the equipment to meet your growing requirement.
Protection
Safety is considered to be most important. With an eye to protect workers from dangerous situation, gas sensors are installed in each dryer zone of the security control equipment. The concentration of gaseous solvents is continuously inspected at the input of the exhaust fan. When the concentration trespass the first level, the system will give an alarm via a siren to the controlling staff. If it trespasses critical level, all functions will stop working. Gas sensors are the masters of the machine.
Resource conserving
The patented dryer technique features a vertical u-shaped web path inside the dryer. This structure makes the machine compact therefore takes up less space: the machinery compartment on its left side containing the ultraprecise coating system and all further web handling components, while the right side is composed of the drying unit(s). That suggest that, it takes up only one third of footprint compared to that of conventional machines. At the same time it is your economical choice. In that respect, easily allows dryers to be made in an explosively safe way, reduces solvent concentration in the dryer exhaust gas, thus eases procuction permits and reduces operation costs. Thanks to our dryer isolation design, which makes the best of energy and keep your working environment neat and tidy.
User friendly
Don’t worry about learning it. There is no complicated operation in our touch panel. Instead of that, you can see the visualization of each coil and stop it just by touching. In terms of safety, this intuitive user interface can reduce the possibility of misoperation. Meanwhile, the training costs will be reduced with the explicit user interface. Nevertheless, the position and angle of the panel can be adjusted. That is to conclude, you can do a series of operations without moving. Thus mitigates the workload. What’s more, the software of the machine includes recipe databank and complies with 21CFR11. That prevents unauthorized persons from entering the system to access electronic records, change and delete electronic records and electronic signatures.
Basic components of machinery compartment standard equipment:
- Three unwinders:
- Wind a carrier foil off: to be coated for the substrate
- Unwind the covering/ protective foil/ backing foil
- Optional unwinder for membrane
- Ultra-precise pump: For precisely feeding the viscous fluid into the coater units
- Optimags patented coating system: A modified dye coater for ultraprecise fluid spreading
- Maximum three rewinders:
- A single or two rewinders is/ are devoted to rewind the final bulkware
- Optional: Further one to rewind arising scrap foil
- Dryer: Patented air circulated oven is composed of up to 12 individual sections/ dryer cabin strung together with an intermediate u-shaped drying technique. Each module contains an upper and a lower dryer zone with individually adjustable temperature and air flow rate.
- Machine control: Siemens S7 PLC , WIN 10 based Human-Machine-Interface (HMI), software includes recipe databank and complies with 21CFR11
PA 1200 Technical specifications
Dryer length | Dimensions LxWxH [m] | Weight [t] | Power supply @ 400V, max. | Coating speed [m/min] | Sections/ zones | Web path geometry through dryer/ Web path length inside the dryer [m] |
---|---|---|---|---|---|---|
4,7m | 8,0 x 2,8 x 2,5 | 8,3 | 100 | 1 | 2 | U-shaped/ 4,7 |
8,5m | 9,6 x 2,8 x 2,5 | 9,8 | 130 | 3,5 | 4 | U-shaped/ 8,5 |
16m | 11,9 x 2,8 x 2,5 | 12,8 | 190 | 6 | 8 | U-shaped/ 16 |
22m | 14,4 x 2,8 x 2,5 | 14,4 | 250 | 8 | 12 | U-shaped/ 22 |
PA 1200 General technical specifications
Foils | Provided as 3” core – coils |
---|---|
Type of handable foils/ webs/ substrates | PET , PP, PVC , paper, non wovens, textiles, …. |
Thickness limitations | > 23 µm for foils > 80 g/m2 for non wovens, textiles, and paper |
Characteristics of foil | Release liner, membranes : Non- elastic, Backings : Non- elastic/ uniaxially elastic |
Foil width | 1200 mm |
Foil coil diameter, maximum | – Release liner: 500 mm – Membrane : 300 mm – Backing : 400 mm |
Coatable fluids | Fed in by dedicated ultra presice pump (s) |
Rheology | – Newtonian fluids – Slightly thixotropic fluids |
Viscosity (static) | 0,1 – 70 Pas |
Coating system | – Patented knife coating system: Modified dye coating system for fluids of viscosity < 7 Pas
achieved dry thickness variation: +/- 1,5 µm
- Doctor Blade: Knife over roll coating system for fluids of viscosity < 70 Pas achieved dry thickness variation: +/- 3,5 µm - Oil coating system: For precise loading of membrane with oil: load >/= 10 g/m2 |
Accepted solvents | Water, Ethanol, Ethylacetate, n-Hexane, n-Heptane, THF,… |
Coating thickness | 40-1000 µm ( dried film ) |
Coating speed | 0.3 – 10 m/ min ( depending on dryer length, refer to the table above) |
Generated/ Final product | ODF: 2 layer , TDS bulks/ laminates: 3- 5 layer |
Measure of film thickness | – Wet film thickness: Fibreoptical sensor DIG 100 – Dry film thickness: Traversing IR sensor NIR |
Dryer | Patented, modul of u-shaped air oven |
Heat supply | Air, HEPA filtered and preheated in own a.h.u. requested fresh air in , max. 3300 Nm3/ h |
Heating in each zone | Electrically from RT -125°C, variance +/- 10C |
Temperature control | By calibrated PT-100 sensor within each dryer |
Recirculating air flow rate in each zone | 100 – 1.100 Nm3/h |
Solvent level control/ alarm | Gas sensors in each dryer zone |
Output in comparison
Optional Accessories
Doctor blade
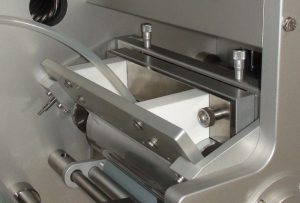
For high viscous fluids
Oil coating station
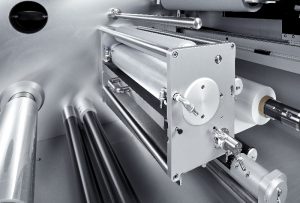
For the manufacturing of matrix patches
Inline slitting station
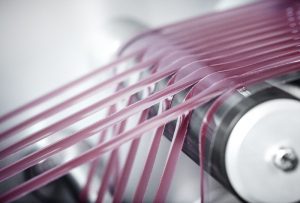
To create inline daughter coils from the primary coil
Wet thickness sensor, DIG 100
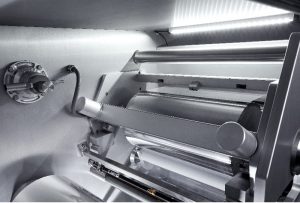
Optical measeurement of wet film thickness right after coating
Dry thickness sensor, NIR
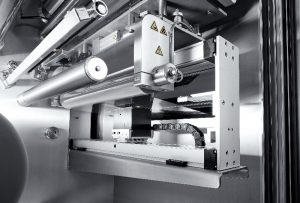
Optical measeurement of dry film thickness with traversing thickness sensor NIR
Optimags GmbH
Dr. Zimmermann
Am Hubengut 8
76149 Karlsruhe
Germany
Phone +49 721 35 285 0
Fax +49 721 35 285 28
c.zimmermann@optimags.de